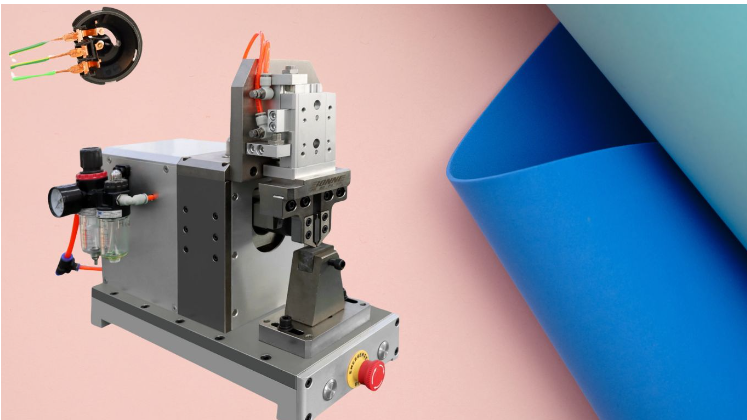
Laser Welding
In the domain of cutting edge assembling and gathering, ultrasonic welding and laser welding are two noticeable advances utilized to get materials together with accuracy and effectiveness. Every technique has its exceptional assets and applications, making them reasonable for various modern requirements. This article gives a far reaching correlation of ultrasonic welding and laser welding, featuring their cycles, benefits, and ideal use cases.
1. Outline of Ultrasonic Welding
Ultrasonic welding is a strong state welding process that utilizes high-recurrence ultrasonic vibrations to join materials. This method principally works with thermoplastic materials, in spite of the fact that it very well may be adjusted for specific metals. The interaction includes the accompanying advances:
Planning: The parts to be welded are set along with exact arrangement.
Utilization of Ultrasonic Vibration: High-recurrence ultrasonic vibrations are applied to the connection point of the parts through a sonotrode or ultrasonic horn. These vibrations produce limited heat because of grinding.
Development of Weld: The intensity relax the material at the point of interaction, making it soften and combine. Pressure is kept up with until the weld sets.
2. Outline of Laser Welding
Laser welding utilizes an engaged laser shaft to soften and join materials. This technique is flexible and can be applied to a large number of materials, including metals, plastics, and composites. The laser welding process includes:
Readiness: The workpieces are adjusted exactly, frequently in a controlled climate.
Utilization of Laser Bar: An extreme focus laser bar is aimed at the joint or crease. The shaft’s energy liquefies the material at the point of interaction.
Hardening: As the laser moves along the joint, the molten material solidifies, forming a strong weld.
3. Key Examinations
a. Interaction and Accuracy
Ultrasonic Welding: This technique is known for its high accuracy and speed. The ultrasonic vibrations give a restricted intensity source, considering exact command over the weld region. This accuracy makes it ideal for fragile parts and little parts, like electronic congregations and clinical gadgets.
Laser Welding: Laser welding offers extraordinary accuracy and control, especially for complex welds and fine subtleties. The laser can be engaged to a tiny spot size, giving exact intensity application and command over the weld profundity and width. This technique is appropriate for applications requiring superior grade, high-strength joints in different materials.
b. Material Similarity
Ultrasonic Welding: The most ideal for thermoplastics and a few metals. It succeeds in getting materials together with low softening focuses or those that don’t need high temperatures for welding. It is especially viable for materials that can be mellowed or softened by ultrasonic energy.
Laser Welding: Exceptionally flexible, fit for welding a great many materials, including metals, plastics, and composites. It is particularly helpful for materials with high dissolving focuses or those requiring high warm information. Laser welding can deal with complex material blends and thicker segments really.
c. Speed and Productivity
Ultrasonic Welding: By and large quicker for little and medium-sized parts because of the fast utilization of ultrasonic energy from the ultrasonic machine. The cycle is constant and doesn’t need broad planning or cooling time, making it proficient for high-volume creation.
Laser Welding: Normally quicker for high-throughput applications, particularly while managing huge or complex parts. The consistent activity and fast laser development consider productive welding over lengthy creases or broad surfaces.
d. Weld Strength and Quality
Ultrasonic Welding: areas of strength for produces solid welds, especially for thermoplastics and meager metal segments. The weld quality relies upon the material properties and the accuracy of the ultrasonic boundaries.
Laser Welding: Conveys high-strength welds with insignificant intensity impacted zones, making it appropriate for high-stress applications. The accuracy and control given by the laser bring about top notch welds with great surface completion and negligible contortion.
4. Optimal Applications
Ultrasonic Welding: Ideal for applications requiring exact, quick, and dependable joining of little parts and fragile parts. Normal purposes incorporate electronic gatherings, clinical gadget producing, and auto parts.
Laser Welding: Appropriate for applications requiring excellent welds in different materials, including metals and plastics. It is usually utilized in enterprises, for example, auto, aviation, gadgets, and gems producing.
5. Cost Contemplations
Ultrasonic Welding: By and large lower introductory hardware costs and functional costs, particularly for little parts and high-volume creation. The ultrasonic machine is energy-productive and requires somewhat low support.
Laser Welding: Higher beginning speculation because of the expense of laser gear. Nonetheless, the flexibility and speed of laser welding can balance these expenses, especially for high-accuracy and high-volume applications.
6. End
Both ultrasonic and laser welding offer particular benefits relying upon the application and material necessities. Ultrasonic welding succeeds in high velocity, exact joining of little parts, especially for thermoplastics. Conversely, laser welding gives flexible, great welds across a scope of materials, making it reasonable for additional complicated and requesting applications.