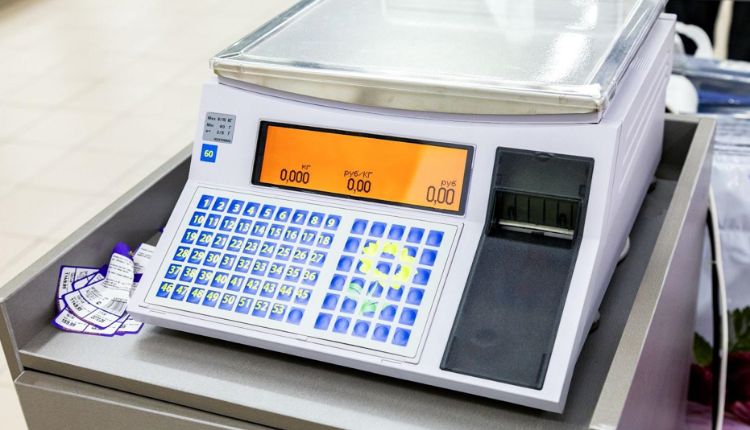
Scale
If you’ve ever worked in a warehouse, manufacturing facility, or even a bustling retail shop, you know how crucial it is to have reliable equipment for counting inventory. As someone who’s spent years helping Australian businesses find the right weighing solutions, I’ve learned that choosing the perfect counting scale isn’t as straightforward as it might seem. Let me share some practical tips that’ll help you make a smart investment.
1: Know Your Capacity Needs
Don’t just think about today – plan for tomorrow! I recently worked with a small electronics components manufacturer in Western Sydney who initially wanted a 5kg scale. After discussing their growth plans, they opted for a 10kg capacity instead. Six months later, they were thankful for the extra capacity as their production doubled. Consider your current needs and add about 20-30% more capacity for future growth.
2: Check the Resolution and Accuracy
Here’s something many people overlook – the resolution of your scale matters more than you might think. For tiny items like screws or electronic components, you’ll need a scale with high resolution (think 0.1g or better). But if you’re counting larger items like automotive parts, you can get by with lower resolution. It’s all about matching the tool to the task, mates!
3: Sample Size Flexibility
A good counting scale should allow you to work with different sample sizes. Sometimes, you might want to count with a sample of 10 pieces; other times, you might want to count 20 or 50 pieces. The more flexible your sampling options, the more accurate your counts will be. I’ve seen this feature save hours of counting time in busy warehouses across Melbourne and Brisbane.
4: Memory and Data Storage
Modern counting scales have come a long way from the basic models of yesteryear. Look for one with memory functions that can store item weights and codes. This feature is particularly handy for businesses that regularly count the same items – no need to weigh sample pieces every time!
5: Interface and Connectivity
In today’s connected world, choosing a digital counting scale that can communicate with your inventory management system can be a game-changer. USB ports, RS-232 interfaces, or even wireless connectivity options can help streamline your operations and reduce manual data entry errors.
6: Power Options
The Australian climate can be unforgiving, and power outages aren’t uncommon in some areas. Consider a scale with both main power and rechargeable battery options. This redundancy can be a lifesaver during those summer storms or unexpected power cuts.
7: Construction and Durability
Look for robust construction that can handle your working environment. If you’re in a dusty warehouse or dealing with moisture, consider IP ratings (water and dust resistance). A sturdy stainless steel platform might cost more initially but will save you money in the long run.
8: Display Quality
The display should be easy to read in various lighting conditions. LED displays are great, but LCD displays with backlight options can be better for brightly lit areas. Make sure the numbers are large enough to read from a comfortable working distance.
9: Calibration and Compliance
In Australia, we have specific trade measurement regulations. If you’re using the scale for trade purposes, ensure it meets National Measurement Institute (NMI) requirements. Regular calibration is essential – look for scales that make this process straightforward.
10: User-Friendly Features
Don’t underestimate the importance of ease of use! Features like tare functions, piece weight entry, and simple menu navigation can make a massive difference in daily operations. I once visited a warehouse in Adelaide where workers were avoiding using their complicated scale – that’s definitely not what you want!
11: After-Sales Support
This is crucial in Australia, where service technicians might not be readily available in all areas. Check if the manufacturer or distributor offers good warranty terms and local support. Quick access to spare parts and technical assistance can minimise downtime.
12: Price vs Value
Despite the temptation to choose the least expensive choice, take ownership costs into account. A quality scale might cost more upfront but saves money through accuracy, reliability, and durability. One of our clients in Perth learned this the hard way after going through three cheaper scales in the time, and they could have had one good one!
Our Takeaway
Understanding these factors will help you make an informed decision when purchasing a counting scale. Remember, the right scale can significantly improve your inventory management efficiency and accuracy. At Meltrons Australia, we’ve seen businesses transform their operations with the right weighing equipment.
Top tip: Before making your final decision, ask for a demonstration or trial period if possible. Nothing beats hands-on experience with the equipment you’ll be using daily. And don’t forget to check if training is provided – even the best scale won’t help if your team doesn’t know how to use it properly!
Remember, investing in quality counting equipment is investing in your business’s efficiency and accuracy. Take your time, do your research, and choose a scale that will serve your needs both now and in the future. Contact Meltrons today!